Introduction
When it comes to optimizing retail shelving, gravity shelf roller tracks offer a game-changing solution. These systems streamline inventory flow, ensuring products stay front-facing and easily accessible to customers. Whether you manage a supermarket, a convenience store, or a retail chain, incorporating these tracks can significantly boost efficiency and improve product presentation.
Why This Guide Matters
This guide walks you through everything you need to know—from setting up roller track systems correctly to understanding how they enhance retail operations. By the end, you’ll have a clear understanding of the installation process and the key advantages of implementing this technology.
Who Should Read This?
If you’re a store manager, retailer, or distributor, this guide is for you. Discover how to make the most of these shelving systems, minimize restocking efforts, and create an organized display that drives more sales.
Understanding Gravity Shelf Roller Tracks
Let’s start with the basics.
A gravity shelf roller track is a smart shelving system designed to keep products moving forward automatically. These tracks use a slight incline, allowing items to glide toward the front as customers take products off the shelf.
This setup ensures shelves always look full and organized without the constant need for manual restocking.
What Are Gravity Shelf Roller Tracks?
Here’s the deal—when products shift forward on their own, it saves time and keeps displays looking great.
These tracks are widely used in:
- Supermarkets for beverages, dairy, and packaged goods.
- Retailers with electronic shelf labels to keep items aligned with price tags.
- Clothing and specialty stores for small packaged accessories.
The goal? Better organization, easier product access, and reduced labor costs.
Key Components of a Gravity Shelf Roller Track System
Before diving into installation, it’s essential to understand the core components:
✅ Roller Tracks – The base structure that allows smooth product movement.
✅ Dividers – Keep products aligned and prevent items from overlapping.
✅ Mounting Brackets (opitonal)– Secure the system in place on shelves.
✅ Angle Adjusters – Help optimize movement speed based on product type.
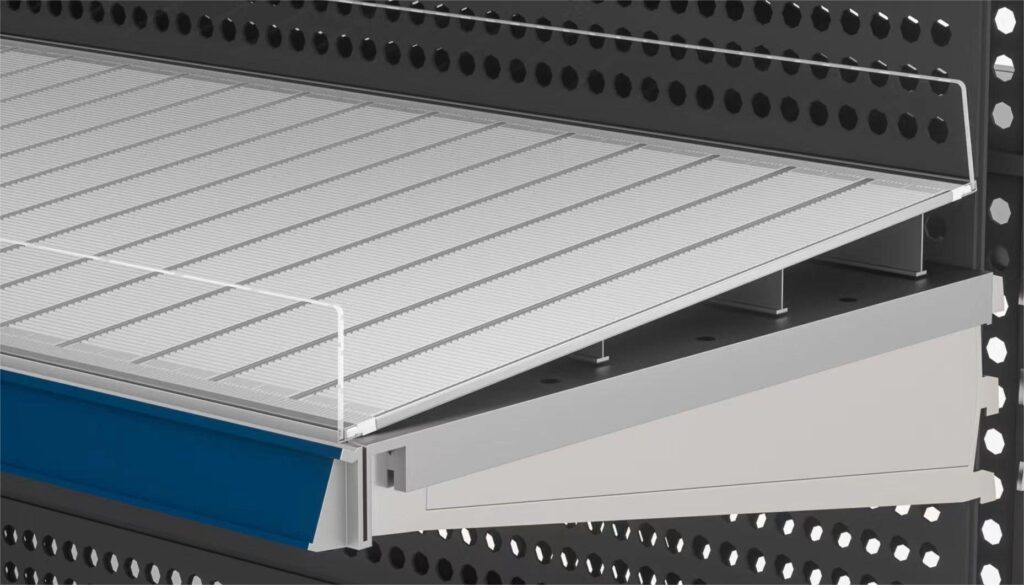
Each part plays a critical role in ensuring a seamless shopping experience and better stock management.
Why Proper Installation Matters
A well-installed track means:
✔️ Smoother product movement without jams or misalignment.
✔️ Less maintenance and fewer operational issues.
✔️ Longer shelf life for your shelving system.
Now that you know why these tracks are essential, let’s move on to what you’ll need to install them.
Tools and Materials Needed for Installation
Before getting started, let’s make sure you have everything ready.
A smooth installation process depends on having the right tools and materials on hand.
Essential Tools for a Hassle-Free Setup
Gather these tools before you begin:
🛠️ Measuring Tape – Ensure correct shelf dimensions.
🛠️ Screwdrivers & Drill – Secure mounting brackets properly.
🛠️ Leveler – Keep the tracks aligned for optimal performance.
🛠️ Angle Finder – Adjust tilt for smooth product movement.
Skipping any of these can lead to misalignment or inefficient product flow.
Choosing the Right Gravity Roller Track for Your Shelves
Not all tracks are the same. Picking the right one depends on:
🔹 Product weight – Heavy items need stronger rollers.
🔹 Shelf width – Measure accurately for a perfect fit.
🔹 Industry needs – Supermarkets and clothing stores may require different setups.
Safety Precautions Before Installation
Safety first!
⚠️ Ensure shelves can support the track system before installation.
⚠️ Avoid overloading to prevent track damage.
⚠️ Secure all screws and brackets tightly to keep everything in place.
With the right tools and precautions, you’re set for a successful installation.
Step-by-Step Installation Guide
Now, let’s get into the actual installation process.
Setting up a roller track system correctly ensures flawless operation and minimal maintenance.
Preparing Your Shelves for Installation
✅ Clear the shelves – Remove any existing items or obstructions.
✅ Measure and mark – Use a tape measure to define where the track will go.
✅ Clean the surface – Dust and debris can affect track adhesion.
Skipping these steps? You might end up with misaligned tracks that don’t function smoothly.
Attaching and Securing the Roller Tracks
🔩 Position the tracks – Align them with the markings.
🔩 Attach the brackets – Secure them tightly with screws.
🔩 Adjust the tilt – Use an angle finder for optimal flow.
Testing and Adjusting for Maximum Performance
Before placing products, test the movement:
✔️ Place a few sample items and check if they move forward smoothly.
✔️ Adjust the incline if items stop mid-way.
✔️ Check for obstructions that might hinder flow.
A little fine-tuning ensures perfect functionality.
Common Installation Mistakes and How to Avoid Them
Even experienced retailers can make mistakes.
Avoid these common pitfalls to keep your system running flawlessly.
Incorrect Alignment Issues
🚫 Problem: Uneven installation leads to slow or stuck products.
✅ Solution: Always use a leveler and double-check before securing screws.
Weight Distribution Problems
🚫 Problem: Overloaded shelves cause roller tracks to bend.
✅ Solution: Stick to the recommended weight limits for smooth movement.
Neglecting Maintenance After Installation
🚫 Problem: Dust buildup can block movement over time.
✅ Solution: Schedule monthly cleanings and check for loose components.
By avoiding these mistakes, you ensure a long-lasting, high-performance setup.
Enhancing Retail Efficiency with Gravity Shelf Roller Tracks
Ready to see the benefits?
A well-implemented track system can revolutionize how retail shelves function.
Faster Stock Rotation and Improved FIFO (First In, First Out)
📦 Why it matters:
- Keeps products fresh, especially in supermarkets.
- Reduces the chance of expired items sitting at the back.
Reducing Manual Restocking Efforts
📉 Less work for employees = More efficiency.
- No more constantly pulling products forward.
- Employees can focus on more valuable tasks.
Preventing Overstocking and Product Clutter
🚀 A cleaner shelf = A better shopping experience.
- Customers can easily find what they need.
- Products remain organized and visually appealing.
With these advantages, it’s clear why retailers are switching to roller track systems.
Cost Savings and Long-Term ROI
Let’s talk about the real impact on your bottom line.
Investing in a gravity-based shelving system might seem like an upfront expense, but the long-term financial benefits are undeniable.
How Gravity Shelf Roller Tracks Reduce Labor Costs
💰 Fewer restocking hours = Lower operational costs.
- Employees spend less time manually adjusting products.
- Retail staff can focus on customer service and inventory management instead.
- Fewer mistakes mean better stock control and less waste.
A one-time investment in roller track shelving can translate into years of savings.
Preventing Product Damage and Loss
🚫 No more damaged goods stuck at the back!
- Smooth front-facing movement reduces crushed packaging.
- Reduces expired product waste by keeping older items accessible.
- A well-organized shelf minimizes customer mishandling.
Maximizing Shelf Space Utilization
📦 Make every inch count.
- Gravity-based flow ensures full product visibility.
- Helps retailers optimize shelf layouts without constant adjustments.
- Prevents clutter and overcrowding, making shopping easier.
By maximizing space and reducing waste, you increase revenue without adding more inventory.
Better Shopping Experience for Customers
Let’s be honest—a well-organized store sells more.
Shoppers are drawn to clean, visually appealing displays where they can easily find what they need.
Easy Access and Better Product Visibility
👀 A clear view = More sales.
- No more hidden products stuck at the back.
- Items stay front-facing, improving visibility.
- Customers make quicker purchase decisions, reducing frustration.
Keeping Shelves Always Organized
🛒 No more messy, out-of-place products.
- Customers prefer a neat, structured layout.
- Prevents items from being pushed back or misplaced.
- Creates a premium shopping experience with minimal staff intervention.
Enhancing the Look of Store Displays
📊 Aesthetics drive sales.
- A cleaner layout increases brand trust.
- Customers are more likely to purchase from well-maintained shelves.
- A professional, well-stocked display makes your store look high-end.
Better organization = Happier customers = Increased revenue.
Ideal Industries and Businesses That Benefit the Most
Who should be using these shelving solutions?
The answer: Any business that sells physical products.
Supermarkets and Grocery Stores
🥦 Freshness and efficiency matter.
- Keeps dairy, beverages, and perishables easily accessible.
- Reduces food waste by maintaining proper stock rotation.
- Makes self-service sections more convenient for shoppers.
Retailers Using Electronic Shelf Labels (ESL)
📡 Syncing price tags with products.
- Prevents items from shifting away from digital price labels.
- Maintains a clean, consistent look on tech-enabled shelves.
- Ideal for stores integrating automation and digital pricing.
Clothing and Specialty Stores
👗 Not just for food!
- Helps organize small packaged accessories, shoes, and folded apparel.
- Creates an aesthetic, easy-to-browse display.
- Improves product rotation, ensuring seasonal items move efficiently.
If your business needs a better way to manage stock and reduce restocking time, these systems are a must-have.
Maintenance and Longevity of Gravity Shelf Roller Tracks
Want your system to stay efficient for years?
Regular upkeep ensures smooth product movement and prevents common issues.
Regular Cleaning and Maintenance Tips
🧼 A little maintenance goes a long way.
- Dust and debris can slow down movement—wipe tracks weekly.
- Check for loose screws and tighten as needed.
- Avoid overloading shelves to prevent excessive wear.
When to Replace or Upgrade Your Tracks
⏳ Know when it’s time for an upgrade.
- If products stop gliding smoothly, tracks may be worn out.
- Visible cracks or warping indicate it’s time for a replacement.
- Switching to stronger or wider tracks can improve heavy-item flow.
Troubleshooting Common Issues
🔧 Simple fixes for common problems.
🚫 Problem: Items getting stuck in the middle.
✅ Solution: Check for blockages or uneven track alignment.
🚫 Problem: Shelves feel unstable.
✅ Solution: Ensure all brackets and mounts are securely tightened.
🚫 Problem: Items move too fast or too slow.
✅ Solution: Adjust the track incline for better control.
Regular check-ups mean fewer breakdowns and better long-term performance.
Final Thoughts
By now, it’s clear—gravity-based shelving is a game-changer for retail efficiency.
🔹 Reduces labor costs and improves stock rotation.
🔹 Keeps products accessible, visible, and front-facing.
🔹 Enhances customer experience while optimizing shelf space.
Investing in smart shelving solutions means less work, fewer losses, and higher sales.
Ready to Upgrade Your Store?
Get in touch for custom solutions, OEM/ODM options, or distribution opportunities.
🚀 Transform your shelving today!